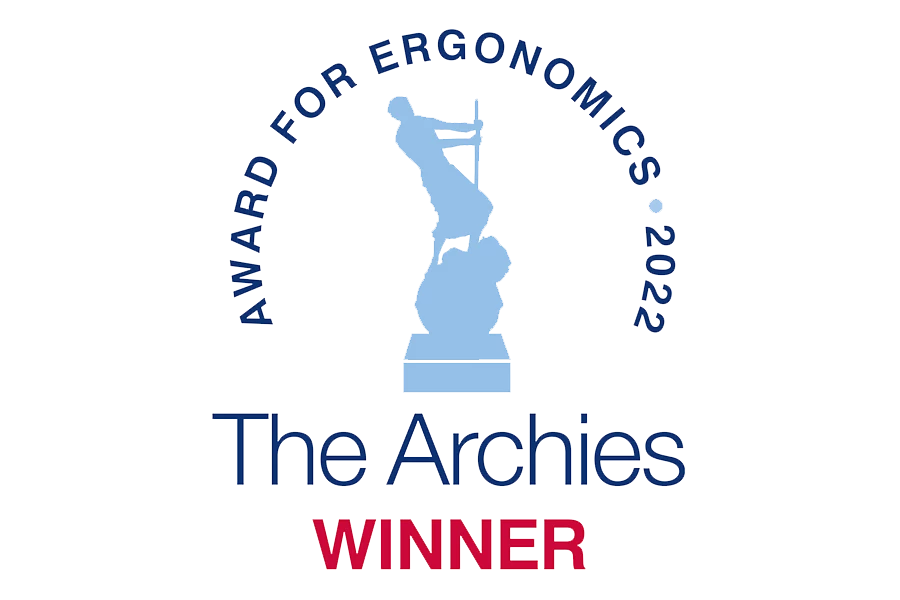
A SERIES
HYSTER A SERIES WINS ERGONOMICS AWARD
The new Hyster® A Series lift trucks won the Ergonomics category at The Archies Awards for Excellence 2022, from the UK Material Handling Association (UKMHA).
The truck has been designed with the operator comfort and productivity in mind and features outstanding upwards visibility and a spacious workplace giving operators greater freedom of movement. With the Hyster A Series, we are delivering tough trucks that are built around the needs of the operator and the intended application.